During his tenure at iconic steam trap manufacturer Barnes & Jones, the company’s former Director of Sales Peter Owens spent a significant percentage of his time observing site inspections. A site inspection entailed visiting a client and manually checking whether or not that client’s steam traps were working properly – that is, minimizing the presence of condensate without losing valuable steam. To execute an inspection, a surveyor would make his or her way to the site, often located in a hard-to-reach, or even hazardous, location. Then, the surveyor would use an ultrasonic handheld probe and a pair of headphones to listen to the sounds the trap made and determine whether or not it was in working order. These tests were run infrequently, and were labor-intensive and limiting.
More critically, the output – sometimes just one data point per trap per year – was far from optimal. “It is probably the most inefficient way to test a steam trap that you can imagine,” says Owens. “What happens if a steam trap fails two weeks after you do the survey? It’s going to sit there and blow wide open for the next 50 weeks. It’s like trying to heat your house with the windows open.”
Beyond the financial, malfunctioning steam traps also have a negative impact on the environment. “Failed traps generate unnecessary gas usage, CO2 pollution, labor utilization, and pipeline infrastructure costs,” says Owens. “There’s definitely a clean energy component to being able to identify failed traps more quickly.”
Owens saw an opportunity for a better solution, so, as he puts it, “I started experimenting.” His goal was to create a test that could identify whether or not a trap was open. Through a trial-and-error process, several potential solutions and systems were discarded one by one. Then, during a Thanksgiving walk in the woods in 2015, Owens had an epiphany.
Utilizing common sensors and microphones, Owens figured out how to create and measure ultrasonic noise, known as a steam trap’s “acoustic signature.” The mechanism was cost-effective and reliable, with one caveat: it was missing a failsafe way to transport the data gathered from the benders back to a system that could make use of it.
“When I approached Northeastern University and said, ‘I’ve got all these sensors – let me use your WiFi to get the data back,’ they said, ‘If you think we’re going to let you put thousands of unsecured devices on our network, you’re crazy!’,” laughs Owens. “The message was, it’s great that you came up with a solution, but you have to find a different way. Once that became clear, LoRaWAN’s range, battery life, cost of components, and capacity of gateways made the decision to go with MachineQ a no-brainer.”
Now, with the help of the MachineQ IoT platform, SteamIQ is in the field, making it possible for companies to collect and analyze each of their steam traps through the lens of one data point per minute, rather than one data point per year. An affordable, easy to install solution, SteamIQ eliminates the need for per-trap surveys, which cost $30 – $40 each, and can identify failing traps essentially instantly, potentially saving tens of thousands of dollars in wasted steam.
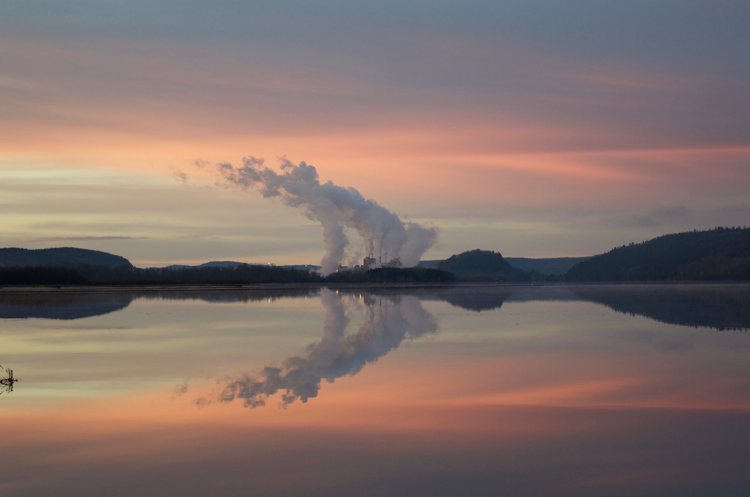
According to the Department of Energy, the failure rate of systems that are not well maintained can range from 10 – 30%. For companies like pharmaceutical companies or breweries that may have “always on” high pressure steam systems comprised of tens of thousands of traps, the cost of stopping production in those instances can be massive. Factoring that in to the loss of steam and the cost of manual surveys even regarding well maintained systems, the cost benefits of SteamIQ are difficult to deny.
Another efficiency comes into play on the repair side. Using SteamIQ, maintenance teams can detect problems immediately. Knowing precisely where a problem is located and when it began enables repair teams to arrive on site with a strong understanding of what the issue likely is. “Now, they don’t have to find the issue, figure out the problem, go back, order the parts to fix it, etc.” says Owens. “Instead, they show up with the right parts, they fix the issue, and they move on.”
SteamIQ is marketed to both utility companies and facilities. According to Owens, MachineQ’s support has played a critical role in the marketing and educational process. “We love those guys,” said Owens. “We are a self-funded startup, but MachineQ trusted us to go out there and prove our technology. They basically said, ‘If you think you can do this, here’s some equipment – go out there and do it.’ That support, right from the start, was invaluable to us.”
Owens notes that the range of the equipment, specifically the private LoRaWAN network, has been critical. “The majority of what we do is deep underground, so having that private backhaul network has given us an enormous advantage,” says Owens.
As SteamIQ monitoring is implemented in major buildings and systems in Boston and New York City, the company is already hard at work on system enhancements and additions. “Because the LoRa technology is readily available, adding additional layers of sensing is quite easy,” says Owens. “For example, monitoring tank levels or hydraulic pressure is now possible. We’re always iterating, and – with the help of MachineQ – trying to find ways to take something that’s as old as the hills and apply advanced technology to make it better.”